“Were I to wait perfection, my book would never be finished.” This quote from Tai K’ung in the thirteenth century is part of the preface to B. F. Brown’s book on stress corrosion cracking. I must quit writing sometime, and that time has come.
This Preface is my opportunity to let readers know what I have attempted to do with this book. In my many years of consulting, teaching, and research, I have been exposed to the oil and gas industry in many countries. The problems are similar, and this book is an attempt to address the most important issues. I have not tried to cover everything important on any given subject; entire books have been written about each of the major subjects. Instead, in this book, I have tried to condense into a concise format:
- Basic principles
- Standards and references for further reading
There are other books on this general subject, and my reason for writing this one is to consolidate into one volume useful information on metallurgy and on the various means of corrosion control.
My own training as a metallurgical engineer prepared me to deal with exotic alloys, but my first two projects in industry after my graduation were on corrosion in concrete and on cathodic protection. From this experience I learned several points that have guided my career and that I have tried to emphasize in this book:
- Most formal education will not cover the specifics useful to a professional’s career.
- Most metals used by industry are carbon and low-alloy steels. This means that protective coatings, chemical treatment using inhibitors and scavengers, and cathodic protection are every bit as important as metallurgy.
There is a saying that goes something like this: “If you want to learn a subject, teach it.” Most of the subjects covered in this book have been suggested by participants in classes I have taught worldwide to industrial audiences. During my career as a professor, I tried to bring into the classroom the lessons taught to me from these industrial courses and from my consulting practice.
Compared with other books on similar subjects, this book has many illustrations, including photographs of problems encountered in the field. It is my hope that these pictures will be useful aids to understanding the subjects under discussion. Many of the illustrations, and the subjects they address, have been suggested by participants in my classes. I always learn more from the classes than I am able to teach. I thank each and every participant for his/her input into how this book was developed.
I have learned over the years that many formally educated corrosion professionals are either engineers or chemists by training. While these two groups represent the largest two categories of backgrounds in the oilfield corrosion control industry, they are in the minority. Those having many other educational backgrounds are also involved in oilfield corrosion control. Most engineers, with the exception of chemical engineers, have little formal education in chemistry, and what chemistry they learned did not emphasize corrosion-related subjects. This is understandable, because most chemistry classes have students from a variety of interests—engineering, agriculture, pharmacy, and so on. It is impossible to emphasize what is important to each field in courses taught to such diversified audiences. Chemists seldom have training in fluid flow, heat transfer, metallurgy, and a variety of other subjects standard to most engineering curricula and important to oilfield problems. I have provided brief chapters emphasizing the corrosion and maintenance aspects of both chemistry and materials. These chapters are intended to be useful for someone needing a refresher to help understand the chapters that follow. Ideas related to corrosion, many of which are not covered in university courses, are also discussed.
The latter chapters of the book are intended to explain field problems and give some insight into how many organizations have addressed these problems. I hope the reader will find them useful.
It is now my opportunity to thank those organizations and people who have helped the most in the preparation of this book.
I have been fortunate to have conducted research or taught classes for all of the “super-major” oil companies and for other companies in a variety of countries. Participation in these classes has taught me what is important to operating company employees, both corrosion professionals and other engineers and technicians who must address corrosion as part of their broader responsibilities.
People who have helped with this book include Charlie Speed, from the NACE New Orleans section, who donated files from industrial courses he has taught on this subject. Jack Smart gave the best talk on corrosion, inspection, and wave loading I have ever heard at the NACE convention in Chicago. This presentation was made the same month as the Alexander Kielland disaster in the North Sea. There is no telling how many lives Jack’s efforts on offshore platform corrosion assessment have saved. Some of Jack’s publications are referenced in this book. Mark Rackley, a pipeliner and an excellent communicator, taught me much about both internal and external corrosion problems. He also did it in an entertaining manner, and that helped to keep the lessons fresh in his audience’s memories. Richard Norsworthy is my other pipeline expert and a much-appreciated colleague. His public questioning of attempts to make cathodic protection unnecessarily complicated are invaluable. When I need coatings advice, I call on Jerry Byrd, and he always helps. Jerry Bauman works for a design firm and taught me the importance of Pitting Resistance Equivalent Numbers (PRENs) for alloys. I also rely on him for other oilfield metallurgy advice. Many oil companies have excellent metallurgy and corrosion groups. When I was at Oklahoma State University, I was fortunate enough to meet and learn from the people at what has become ConocoPhillips. Mike Joosten, Juri Kolts, Jay Murali, Mamdouh Salama, and Bill Thomason have all taught me important lessons that are reflected in this book.
Most of the people mentioned above had training as engineers or chemists. Their contributions to this book have been important. The hundreds of technicians, most of whom I cannot identify, who taught me what really happens in the field, have made even greater contributions to this book. I thank them all.
This book would have never been written without the support and encouragement of Dianne Heidersbach, my wife of 47 years. I thank her most of all.
BOB HEIDERSBACH
Cape Canaveral, Florida
May 2010
1
INTRODUCTION TO OILFIELD METALLURGY AND CORROSION CONTROL
The American Petroleum Institute (API) divides the petroleum industry into the following categories:
- Upstream
- Downstream
- Pipelines
Other organizations use terms like production, pipelining, transportation, and refining. This book will discuss upstream operations, with an emphasis on production, and pipelines, which are closely tied to upstream operations. Many “pipelines” could also be termed gathering lines or flowlines, and the technologies involved in materials selection and corrosion control are similar for all three categories of equipment.
Until the 1980s, metals used in upstream production operations were primarily carbon steels. Developments of deep, hot gas wells in the 1980s led to the use of corrosion-resistant alloys (CRAs), and this trend continues as the industry becomes involved in deeper and more aggressive environments.1 Nonetheless, the most used metal in oil and gas production is carbon steel or low-alloy steel, and nonmetallic materials are used much less than metals.
Increased emphasis on reliability also contributes to the use of newer or more corrosion-resistant materials. Many oil fields that were designed with anticipated operating lives of 20–30 years are still economically viable after more than 50 years. This life extension of oil fields is the result of increases in the market value of petroleum products and the development of enhanced recovery techniques that make possible the recovery of larger fractions of the hydrocarbons in downhole formations. Unfortunately, this tendency to prolong the life of oil fields creates corrosion and reliability problems in older oil fields when reductions in production and return on investment cause management to become reluctant to spend additional resources on maintenance and inspection.
These trends have all led to an industry that tends to design for much longer production lives and tries to use more reliable designs and materials. The previous tendency to rely on maintenance is being replaced by the trend to design more robust and reliable systems instead of relying on inspection and maintenance. The reduction in available trained labor for maintenance also drives this trend.
COSTS
A U.S. government report estimated that the cost of corrosion in upstream operations and pipelines was $1372 billion per year, with the largest expenses associated with pipelines followed by downhole tubing and increased capital expenditures (CRAs, etc.). The most important opportunity for savings is the prevention of failures that lead to lost production. The same report suggested that the lack of corrosion problems in existing systems does not justify reduced maintenance budgets, which is a recognition that as oil fields age, they become more corrosive at times when reduced returns on investment are occurring.2 It is estimated that corrosion costs are approximately equal to mechanical breakdowns in maintenance costs.
SAFETY
While proper equipment design, materials selection, and corrosion control can result in monetary savings, a perhaps more important reason for corrosion control is safety. Hydrogen sulfide, H2S, is a common component of many produced fluids. It is poisonous to humans, and it also causes a variety of environmental cracking problems. The proper selection of H2S-resistant materials is a subject of continuing efforts, and new industrial standards related to defining metals and other materials that can safely be used in H2S-containing (often called “sour”) environments are being developed and revised due to research and field investigations.
Pipelines and other oilfield equipment frequently operate at high fluid pressures. Crude oil pipelines can leak and cause environmental damage, but natural gas pipeline leaks, like the corrosion-related rupture in Carlsbad, New Mexico, shown in Figure 1.1, can lead to explosions and are sometimes fatal.3 High-pressure gas releases can also cause expansive cooling leading to brittle behavior on otherwise ductile pipelines. API standards for line pipe were revised in 2000 to recognize this possibility. Older pipelines, constructed before the implementation of these revised standards, are usually made from steel with no controls on low-temperature brittle behavior and may develop brittle problems if they leak. Gas pipelines are more dangerous than liquid pipelines.
ENVIRONMENTAL DAMAGE
Environmental concerns are also a reason for corrosion control. Figure 1.2 shows oil leaking from a pipeline that suffered internal corrosion followed by subsequent splitting along a longitudinal weld seam. The damages due to this leak are minimal compared with the environmental damages that would have resulted if the leak had been on a submerged pipeline. Figure 1.3 shows an oil containment boom on a river where a submerged crude oil pipeline was leaking due to external corrosion caused by non-adherent protective coatings that shielded the exposed metal surfaces from protective cathodic protection currents.
CORROSION CONTROL
The environmental factors that influence corrosion are:4
- CO2 partial pressure
- H2S partial pressure
- Fluid temperature
- Water salinity
- Water cut
- Fluid dynamics
- pH
Corrosion is normally controlled by one or more of the following:
- Material choice
- Protective coatings
- Cathodic protection
- Inhibition
- Treatment of environment
- Structural design including corrosion allowances
- Scheduled maintenance and inspection
Figure 1.4 shows an offshore platform leg in relatively shallow water, approximately 30 m (100 ft) deep, in Cook Inlet, Alaska. The leg is made from carbon steel, which would corrode in this service. Corrosion control is provided by an impressed current cathodic protection system. The bottom of the leg is 2.5 cm (1 in.) thicker than the rest of the leg, and this is intended as a corrosion allowance for the submerged portions of the platform legs. Note that the water level goes above the corrosion allowance twice a day during high tides, because the platform is located in water 3 m (10 ft) deeper than was intended during design and construction. Fortunately, the cathodic protection system was able to provide enough current, even in the fast-flowing abrasive tidal waters of Cook Inlet, to control corrosion. This platform was obsolete when the picture was taken, but it was less expensive to operate and maintain the platform than it was to remove it. Thirty-five years later, oil prices had increased, recovery methods had improved, and the platform was economically profitable. Robust designs, adequate safety margins, and continuous re-evaluation of corrosion control methods are important, not just for marine structures, but for all oilfield equipment.
REFERENCES
1 R. Kane. 2006. Corrosion in Petroleum Production Operations, Metals Handbook, Vol. 13C—Corrosion: Corrosion in Specific Industries. Metals Park, OH: ASM International. 922–966.
2 G. Ruschau and M. Al-Anezi. 2001. Oil and gas exploration and production. Appendix S to Corrosion Costs and Preventive Strategies in the United States, Report FHWA-RD-01-156, September 2001.
3 NTSB. 2003. Pipeline Accident Report, Natural gas pipeline rupture and fire near Carlsbad, New Mexico, August 19, 2000. National Transportation Safety Board, NTSB/PAR-03/01, February 11, 2003.
4 Iranian Petroleum Standard, 1997. IPS-E-TP-760. Corro‑sion control in design. http://igs.nigc.ir/IPS/tp/e-tp-760.pdf (accessed May 1, 2010).
Corrosion, the degradation of a material due to reaction(s) with the environment, is usually, but not always, electrochemical in nature. For this reason, an understanding of basic electrochemistry is necessary to the understanding of corrosion. More detailed descriptions of all phenomena discussed in this chapter are available in many general corrosion textbooks.1–8
ELECTROCHEMISTRY OF CORROSION
Most corrosion involves the oxidation of a metal which is accompanied by equivalent reduction reactions which consume the electrons associated with the corrosion reaction. The overall corrosion reactions are often referred to separately as “half-cell” reactions, but both oxidation and reduction are interrelated, and the electrical current of both anodes, where oxidation is prevalent, and cathodes, where reduction predominates, must be equal in order to conserve electrical charges in the overall system.
Electrochemical Reactions
A typical oxidation reaction for carbon steel would be:
(Eq. 2.1)
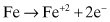
Common reduction reactions associated with corrosion include:
(Eq. 2.2)

Oxygen reduction
(Eq. 2.3)

(Eq. 2.4)

Metal ion reduction or deposition is also possible:
(Eq. 2.5)

(Eq. 2.6)

The reduction reaction is usually corrosion-rate controlling because of the low concentrations of the reducible species in most environments compared with the high concentration (essentially 100%) of the metal. As one example, the dissolved oxygen concentration in most air-exposed surface waters is slightly lower than 10 ppm (parts per million). This relatively low dissolved oxygen concentration is usually much higher than the concentration of any other reducible species, and the control of air leakage into surface facilities is a primary means of controlling internal corrosion in topside equipment and piping.
More than one oxidation or reduction reaction may be occurring on a metal surface, for example, if an alloy is corroding or if an aerated acid has high levels of dissolved oxygen in addition to the hydrogen ions of the acid.
Electrochemical reactions occur at anodes, locations of net oxidation reactions, and at cathodes, locations of net reduction reactions. These anodes and cathodes can be very close, for example different metallurgical phases on a metal surface, or they can have wide separations, for example, in electrochemical cells caused by differences in environment or galvanic cells between anodes and cathodes made of different materials.
Electrolyte Conductivity
The electrical conductivity of an environment is determined by the concentration of ions in the environment, and the resulting changes in corrosivity can be understood by considering Ohm’s Law:
(Eq. 2.7)

where:
E = the potential difference between anode and cathode, measured in volts
I = the electrical current, measured in amperes
R = the resistance of the electrical circuit, determined by the distances between anode and cathode and by ρ, the resistivity of the electrolyte, which is usually expressed in ohm-centimeters (Ω-cm). In most cases, the distance between anode and cathode is not known, but the changes in the corrosion rate can be monitored and correlated in changes in resistivity, for example, the changes in resistivity of soils caused by changes in moisture content which alter the ionic content of the soil electrolyte.
The resistivity of liquids and solids is determined by the ions dissolved in the bulk solution. Hydrocarbons such as crude oil, natural gas, and natural gas condensates are covalent in nature and are very poor electrolytes because they have very high resistivities. Oilfield corrosion is usually caused by chemicals in the water phase that, among other things, lower the natural resistivity of water, which is also mostly covalent. Water is a very efficient solvent for many chemicals, and most oilfield corrosion occurs when metal surfaces become wetted by continuous water phases having dissolved chemicals which lower the natural high resistivity (low conductivity) of water.
Faraday’s Law of Electrolysis
The mass of metal lost due to anodic corrosion currents can be determined from Faraday’s law for electrolysis, Equation 2.8, which is also used by the electroplating industry:
(Eq. 2.8)
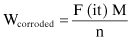
where:
Wcorroded = mass (weight) of corroded/electrodeposited metal
F = Faraday’s constant
i = current in amps
t = time of current passage
m = molar mass of the element in question
n = ionic charge of the metal in question
The amount of a substance consumed or produced at one of the electrodes in an electrolytic cell is directly proportional to the amount of electricity that passes through the cell. Methods of measuring the corrosion current are difficult and are discussed in Chapter 7, Inspection, Monitoring, and Testing.
Electrode Potentials and Current
The Electromotive Force (EMF) Series is an orderly arrangement of the relative standard potentials for pure metals in standard, unit activity (1 Normal, 1 N), solutions of their own ions (Table 2.1). The more active metals on this list tend to be corrosion susceptible and the less active, or noble metals, will resist corrosion in many environments.
TABLE 2.1 The Electromotive Force Series for Selected Metals
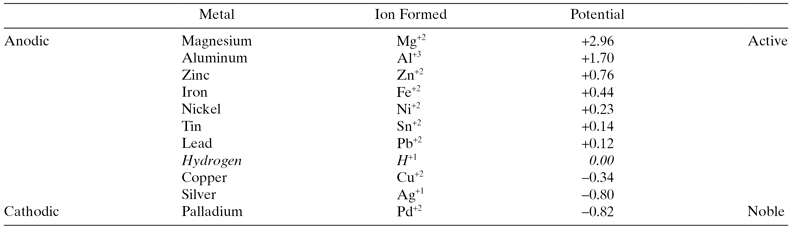
Source: Adapted from M. Parker and E. Peattie, Pipeline Corrosion and Cathodic Protection, 3rd ed. (Gulf Publishing, Houston, TX, 1984; 1995 reprinting), p. 157.
It should be noted that two sign conventions are followed in publishing the EMF series. This can cause confusion, which can be avoided if the reader understands that active metals like magnesium and aluminum will always be anodic to carbon steel, and corrosion-resistant metals like silver and palladium will be cathodic.
The EMF series shows equilibrium potentials for pure metals in 1 N (one normal or unit activity of ions) solutions of their own ions. While this is the basis for much theoretical work in corrosion and other areas of electrochemistry, pure metals are seldom used in industry, and oilfield corrosive environments never have 1 N metal ion concentrations. The more practical galvanic series (Figure 2.1), which shows the relative corrosion potentials of many practical metals, is often used in corrosion control. This is based on experimental work in seawater and serves as the basis for many corrosion-related designs.
The galvanic series in seawater shown in Figure 2.1 is widely used for engineering designs. Some authorities claim that the relationships between various alloys must be determined for each environment, but this is seldom done. The reason for this precaution is that zinc and carbon steel undergo a polarity reversal in some freshwaters at approximately 60°C (140°F). The only other polarity reversal that has been reported is when tin, which would normally be cathodic to carbon steel, becomes anodic to carbon steel in deaerated organic acids, such as are found in the common tin cans used for food storage. It is unlikely that any other polarity reversals will be found in oilfield environments, and designers should assume that the relationships shown in Figure 2.1 are valid. Revie and Uhlig offer a brief review of polarity reversals.2
The Nernst equation, first published in 1888 by the German chemist who later won the 1920 Nobel Prize in chemistry, explains how potentials of both anodic and cathodic reactions can be influenced by changes in the temperature and chemical compositions of the environment. The reduction potential can be expressed as:
(Eq. 2.9)

where:
E = the electrochemical potential of the reaction in question
E° = the standard electrode potential at 25°C in a 1 N solution of the ion formed by oxidation of the reactants in question
R = the universal gas constant = 8.31 Joules/gram mole K
T = the absolute temperature, Kelvin
n = the charge on the ion being reduced
F = Faraday’s constant = 96,500 coulombs/gram-equivalent
At standard temperature conditions, this equation can be simplified to:
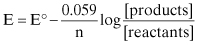
The details of this relationship are described in many general corrosion textbooks.1–7 What is important to understand for oilfield corrosion control is that electrochemical cells (corrosion cells) can be caused by changes in:
- Temperature
- Chemical concentrations in the environment
Both types of electrochemical cells are important in oilfield corrosion and will be discussed further in Chapter 5, Forms of Corrosion.
It is simplistic to describe a chemical reaction as either oxidation or reduction. In actuality, the reversible chemical reactions are happening in both directions simultaneously. The equilibrium potential, determined by the Nernst equation, is the potential where the oxidation and reduction currents, measured in current density on an electrode surface, are equal. The current density at this point is called the exchange current density. Some metals, for example, the platinum and palladium used in impressed current anodes, have very high exchange current densities. This means that a small surface area of these materials can support much higher anodic currents than other anode materials such as high-silicon cast iron or graphite. Figure 2.2 shows exchange current densities for hydrogen oxidation/reduction reactions. A platinum surface can support 10,000 times the current density of an iron anode for the same reaction. This increase in efficiency is used in the cathodic protection industry to justify the use of relatively expensive precious metal surfaces to replace much heavier, and therefore harder to install, high-silicon cast iron anodes.
As potentials change from the equilibrium potential, the electrode surface becomes either an anode or a cathode. It is common to plot the shifts in potential on linear-logarithmic plots because in many cases, these plots produce a region of activation-controlled electrode behavior where the voltage of anodes and cathodes follows a log-linear pattern, called the Tafel slope, after the German scientist who first explained this behavior in 1905.
On an anode, the Tafel equation can be stated as:
(Eq. 2.10)
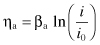
where:
ηa = the overpotential, or change between the measured potential and the potential at the current density of interest. The subscript “a” indicates that this polarization is “activation polarization” which occurs at low current densities near the equilibrium potential.
βa = the so-called “Tafel slope”
i = the current density, A/m2
i0 = the exchange current density, A/m2.
At low electrode current densities, the change in potential can be plotted as shown in Figure 2.3. These plots of potential versus logarithm of current are often termed Evans diagrams, after Professor U. R. Evans of Cambridge University, who popularized their use.5
As stated above, most oilfield corrosion rates are controlled by the low concentrations of reducible species in the environment. These species must migrate, or diffuse, to the metal surface in order to react. The rate of this diffusion is controlled by the concentration of the diffusing species in the environment, the thickness of the boundary layer where this diffusion is occurring (largely determined by fluid flow or the lack thereof), temperature, and other considerations. The resulting concentration polarization can be written as:
(Eq. 2.11)
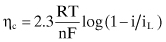
where:
ηc = the overpotential, or polarization, caused by the diffusion of reducible species to the metal surface
F = Faraday’s constant
i = the current on the electrode
iL = the limiting current density determined by the diffusivity of the reducible species; this is the maximum rate of reduction possible for a given corrosion system
The other terms are the same as described above in discussions of the Nernst equation and activation polarization (Tafel slope) behavior.
Concentration polarization is shown in Figure 2.4. In corrosion, the limited concentrations of reducible species produce concentration polarization only at cathodes. At low current densities, the concentration polarization is negligible, and, as the reduction current density approaches the limiting current, the slope quickly becomes a vertical downward line.
The total polarization of an electrode is the sum of both the activation and concentration polarization. The combined polarization for a reduction reaction on a cathode is:
(Eq. 2.12)

This is shown in Figure 2.5.
As stated earlier, most oilfield corrosion rates are determined by the concentration of the reducible chemicals in the environment. Figure 2.6a shows how the polarization of both the oxidation of a metal and the reduction of hydrogen ions determines the corrosion rate, icorr, and the corrosion potential, Ecorr for a generic metal.
For surface equipment, most corrosion rates are determined by the concentration of dissolved oxygen in whatever water is available. This is shown in Figure 2.6b, where the oxidation line showing Tafel behavior intersects the vertical (concentration limited) portion of the reduction reaction.
The importance of potential in determining corrosion rates is apparent from the above discussions. Academic chemistry reports tend to describe potentials relative to the standard hydrogen electrode, which has been arbitrarily set to a potential of zero. In field applications, it is common to use other reference electrodes. The most common reference electrodes used in oilfield work are the saturated copper-copper sulfate electrode (CSE), used in onshore applications, and the silver-silver chloride electrode used for offshore measurements, where contamination of the CSE electrode would produce variable readings. Table 2.2 shows conversion factors for these electrodes and other commonly used reference electrodes compared with the standard hydrogen electrode (SHE). As an example, an electrode which measures −0.300 V versus CSE would measure +0.018 V versus SHE. Figure 2.7 shows a standard copper-copper sulfate electrode.
TABLE 2.2 Potential Values for Common Reference Electrodes
|
|
Copper-copper sulfate | +0.318 |
Saturated calomel | +0.241 |
Silver-silver chloride | +0.222 |
Standard hydrogen | +0.000 |
Adapted from Reference 3.
CORROSION RATE EXPRESSIONS
Corrosion rates are measured in a number of ways:
- Depth of penetration
- Weight loss
- Electrical current associated with corrosion
- Time to failure
The simplest of these concepts to understand is depth of penetration. It can be expressed in mm/yr (millimeters per year) or mpy (mils or thousandths of an inch per year). The loss of wall thickness is often used to determine remaining equipment life or safe operating pressures for piping systems, storage tanks, and so on. Table 2.3 shows a commonly used classification of relative corrosion rates. The U.S. Standard units, mpy, produce small numbers that are easy to understand, and corrosion rates in mpy are commonly used worldwide, although other expressions are also common.1
TABLE 2.3 Relative Corrosion Resistance versus Annual Penetration Rates
|
|
Outstanding | <1 | <0.02 |
Excellent | 1–5 | 0.02–0.1 |
Good | 5–20 | 0.1–0.5 |
Fair | 20–50 | 0.5–1 |
Poor | 50–200 | 1–5 |
Unacceptable | 200+ | 5+ |
Source: Adapted from M. Fontana, Corrosion Engineering (McGraw-Hill, 1986).1
Weight loss measurements are commonly used on exposure samples used to monitor corrosion rates in oil and gas production. It is a simple matter to convert these weight loss measurements into average depths of penetration, although this can be very misleading, because most corrosion is localized in nature and the average penetration rate seldom gives an indication of the true condition of oilfield equipment.
The electrical current associated with anodic dissolution of a metal can be used to determine the corrosion rate using Faraday’s law. This calculation of mass loss can be converted into remaining thickness. Once again, the reader is cautioned that most corrosion is localized in nature and calculations assuming uniform loss of cross section are frequently misleading.
The time to failure, however defined, is the most common concern of managers and operators of equipment. For some forms of corrosion testing, for example, stress corrosion cracking, the time to failure is used to screen alloys, environments, or other variables.
pH
The pH of an environment is one of the major factors determining if corrosion will occur. It also influences the type of corrosion that is experienced.
pH is defined as:
(Eq. 2.13)
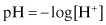
where the [H+] expression shows the hydrogen ion activity of the environment.
The [H+] depends on the ionization of water and varies with temperature. The pH of neutral water at standard temperature (25°) is 7.00, but neutrality varies with temperature as shown in Figure 2.8. Downhole oilfield temperatures are usually elevated, and it is common to calculate the in situ pH of any fluids that might affect corrosion or scale deposition. There are many software packages available for this purpose. Figure 2.9 shows the effects of pH on the corrosion rates of iron in water. At low pHs, bare metal is exposed to the environment, and acid reduction on the surface controls corrosion rates. For intermediate pHs, a partially protective film of iron oxide reduces the corrosion rate and the diffusion of oxygen to cathodic locations on the metal surface controls. As the pH increases to even higher values, the surface becomes covered with mineral scales and corrosion is reduced.
PASSIVITY
Passivity is a phenomenon that is frequently misunderstood. Most metals form oxide films in most corrosive environments. These passive films can be protective and retard or even effectively stop corrosion, but they can also lead to fairly deep localized corrosion in situations where the protective films are removed or defective. Except in rare circumstances, the oxide films formed on carbon steel are not adequately protective, and other means of corrosion control are necessary. This is in contrast to stainless steels, titanium, and aluminum—oilfield metals that form protective passive films which are commonly the primary means of corrosion control for these alloys. On many corrosion-resistant alloys such as stainless steels, the passive films may be only dozens of atoms thick. This means that they are very weak and are subject to mechanical damage, and this can lead to localized corrosion at the damaged locations.
Potential-pH (Pourbaix) Diagrams
Marcel Pourbaix developed a means of explaining the thermodynamics of corrosion systems by plotting regions of thermodynamic stability of metals and their reaction plots on potential versus pH plots.10–12 The regions of a Pourbaix diagram can be described as:
- Immunity The metal cannot oxidize or corrode (although it may still be subject to hydrogen embrittlement).
- Corrosion Ions of the metal are thermodynamically stable and the metal will corrode.
- Passivity Compounds of the metal and chemicals from the environment are thermodynamically stable, and the metal may be protected from corrosion if the passive film is adherent and protective.
Many users of Pourbaix diagrams miss the final point above. Thermodynamics alone cannot predict if passive films will be protective or not.2,11–14
Figure 2.10 shows the Pourbaix diagram for water. Water is thermodynamically stable over a potential region of 1.23 V, and the potentials at which oxidation and evolution (bubbling off) of oxygen from water at the top of the diagram or the evolution of hydrogen at the bottom of the diagram depend on the pH of the environment.
The Pourbaix diagram of iron is superimposed on the diagram for water in Figure 2.11. Similar diagrams are available for most structural metals for which thermodynamic data are available (Figure 2.11).2,11–14
These diagrams make a number of important points useful for oilfield corrosion control:
- Water is only stable over a potential range of slightly more than one volt. This is very important in cathodic protection.
- Iron (carbon steel) is covered with iron oxides (passive films) in most aqueous environments. Unfortunately, these passive films are usually not sufficiently protective and other means of corrosion control are necessary.
- The potentials at which iron (carbon steel) is protected from corrosion do not coincide with the immunity regions on the Pourbaix diagram. This point is discussed in greater detail in Chapter 6, Corrosion Control.
The diagrams for zinc, aluminum, and cadmium, commonly referred to as the amphoteric coating metals, have passive regions in neutral environments. These metals also have low corrosion rates in neutral environments and higher corrosion rates in both acids and bases.
Pourbaix diagrams have limitations in addition to the inability of thermodynamics to predict the protectiveness of passive films. These include the idea that they can only be calculated for alloys, although experimental Pourbaix diagrams have been reported.12,13 Revie and Uhlig list other limitations.2
SUMMARY
The following ideas have been discussed in detail in this chapter:
- Corrosion is electrochemical in nature.
- Most metal surfaces have both oxidation and reduction occurring simultaneously.
- If the predominant reaction is oxidation, the metal will corrode.
- The most important reduction reaction is oxygen reduction for many oilfield systems. If no oxygen is available, the corrosion rate will often be very low.
Electrode potentials are determined by:
- Metal chemistry
- Chemicals in the environment
- Temperature
These potentials are usually measured against either copper-copper sulfate or silver-silver chloride electrodes, depending on the environment.
Corrosion rates are often expressed by average depth of penetration, and this can be misleading because most oilfield corrosion is localized in nature.
The pH of the environment has a major effect on corrosivity.
Passive films may limit corrosion in many environments, but carbon steel, the most common oilfield metal, seldom forms adequately protective passive films, and other means of corrosion are often necessary.
REFERENCES
1 M. Fontana. 1986. Corrosion Engineering. New York: McGraw-Hill.
2 W. R. Revie and H. H. Uhlig. 2008. Corrosion and Corrosion Control. New York: Wiley-Interscience.
3 D. A. Jones. 1996. Principles and Prevention of Corrosion, 2nd ed. Upper Saddle River, NJ: Prentice-Hall.
4 P. R. Roberge. 2006. Basics—An Introduction, 2nd ed. Houston, TX: NACE International.
5 Z. Ahmad. 2006. Principles of Corrosion Engineering and Corrosion Control. Oxford: Butterworth-Heinemann.
6 S. A. Bradford. 2001. Corrosion Control, 2nd ed. Edmonton, Alberta, Canada: CASTI.
7 K. R. Trethewey and J. Chamberlin. 1995. Corrosion for Science and Engineering, 2nd ed. London: Longman Scientific and Technical.
8 E. McCafferty. 2009. Introduction to Corrosion Science. Berlin: Springer-Verlag.
9 J. Beavers. 2000. Fundamentals of corrosion. In Peabody’s Control of Pipeline Corrosion, 2nd ed., ed. R. Bianchetti, 297–317. Houston, TX: NACE International.
10 R. Baboian, ed. 2002. Corrosion Engineer’s Reference Book, 3rd ed. Houston, TX: NACE International, 78.
11 M. Pourbaix. 1974. Atlas of Electrochemical Equilibria in Aqueous Solutions, 2nd English ed. Houston, TX: National Association of Corrosion Engineers, and Brussels: Centre Belge d’Etude de la Corrosion (CELBECOR).
12 E. D. Verink Jr. 2000. Simplified procedure for constructing Pourbaix diagrams. In Uhlig’s Corrosion Handbook, 2nd ed., ed. R. W. Revie, 111–124. New York: Wiley-Interscience.
13 W. T. Thompson, M. H. Kaye, C. W. Bale, and A. D. Pelton. 2000. Pourbaix diagrams for multielement systems. In Uhlig’s Corrosion Handbook, 2nd ed., ed. R. W. Revie, 125–136. New York: Wiley-Interscience.
14 B. Cottis. 2002. Introduction to corrosion, UMIST Corrosion and Protection Centre. http://corrosiontest.its.manchester.ac.uk/lecturenotes/civils/Civils%20
Corrosion%20Notes.pdf (accessed May 28, 2009).