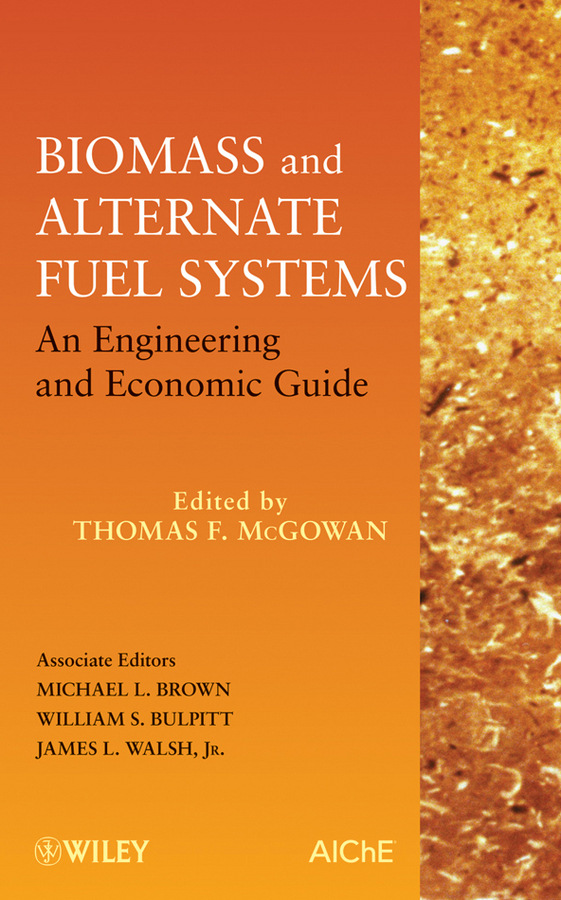
CONTENTS
Preface
Acknowledgments
Chapter 1: Introduction to Alternate Fuels
Introduction
What Fuels Are Used?
Combustion Issues And Application To Equipment
About Emissions And Regulations
References
Chapter 2: Fuel Properties and Combustion Theory
It’s All About Combustion
Combustion Basics
Biomass Fuels
Agricultural Feedstocks
Sustainability Of Wood Fuels
References
Chapter 3: Liquid Fuels from Biomass
Introduction
Vegetable Oil And Biodiesel
Alcohol From Biomass
References
Chapter 4: Biomass Combustion EquipmentSteam, Hot Oil, and Hot Gas
Boiler Types
Wood-Fired Package Boilers—Manufacturers
Hot Oil Systems
Production Of Hot Gas From Biomass
Combined Systems: Hot Gas And Thermal Oil
Fluidized-Bed Combustors
Burners And Furnaces
Furnaces For Burning Biomass
Pyrolysis Systems
Wood Gasifiers
Other Combustion Systems
Ash Slagging And Slag Conrol
References
Chapter 5: Biomass Fuel Storage and Handling
Solids Handling Fuel Properties
Receiving
Storage
In-Plant Fuel Handling
Preparation Of Wood Fuel
Dryers
Appropriate Applications Of Dryers
Typical Designs Of Wood Fuel Facilities
References
Chapter 6: Cogeneration and Power Generation
Introduction
Government Incentives
Steam Turbines
Economic Considerations
Cogeneration System Size
Reference
Chapter 7: Emissions and Control
Introduction
Types Of Emission
Emission Regulations
Expected Emissions
Control Techniques
Costs
References
Chapter 8: Environment and Safety: Rules, Regulations, and Safe Practice
Environmental Impact
Pertinent Environmental Regulations
Mact
Safety
Chapter 9: Biomass Fuel Supply and Purchasing
Determining Fuel Supply
Purchasing And Contracting For Wood Fuels
Chapter 10: Fuel-Switching Feasibility Study Methodology
Energy Requirements
System And Fuel Requirements
Existing System And Site Data
Facility Layout
Operational Requirements
Economic Analysis
Installation Planning
Chapter 11: Economic Analysis of Biomass Combustion Systems
Tax Considerations
Chapter 12: Biomass Fuel Processing Routes and Economics
Introduction
Economic Analysis
Processing Routes
Biomass-Derived Fuels
Densified Wood And Wood Pellet Production
Direct Combustion For Steam Generation
Summary
References
Chapter 13: Biomass Fuel Processing Network
Chapter 14: Example Feasibility Study: Nonforest Products Facility
Background
Conceptual Design
Wood Fuel Availability
Contractor Selection
System Description
Feasibility Studies
Operations
Appendix 1: Equipment Manufacturers/Vendors Listing
Appendix 2: State Forestry Commission Offices
Appendix 3: Glossary
Index
Disclaimer: The contents of this book are offered as guidance. The editors and authors and all technical sources referenced herein do not (a) make any warranty of representation, expressed or implied, with respect to the accuracy, completeness, or usefulness of the information contained in this text, or that the use of any information, apparatus, method, or process disclosed in this text may not infringe on privately owned rights; (b) assume any liabilities with respect to the use of, or for damages resulting from the use of, any information, apparatus, method, or process disclosed in this text. Mention of trade names or commercial products does not constitute endorsement or recommendation.
Copyright © 2009 American Institute of Chemical Engineers, Inc. All rights reserved.
A Joint Publication of the American Institute of Chemical Engineers, Inc. and John Wiley & Sons, Inc.
Published by John Wiley & Sons, Inc., Hoboken, New Jersey Published simultaneously in Canada.
No part of this publication may be reproduced, stored in a retrieval system or transmitted in any form or by any means, electronic, mechanical, photocopying, recording, scanning or otherwise, except as permitted under Section 107 or 108 of the 1976 United States Copyright Act, without either the prior written permission of the Publisher, or authorization through payment of the appropriate per-copy fee to the Copyright Clearance Center, Inc., 222 Rosewood Drive, Danvers, MA 01923, (978) 750-8400, fax (978) 750-4470, or on the web at www.copyright.com. Requests to the Publisher for permission should be addressed to the Permissions Department, John Wiley & Sons, Inc., 111 River Street, Hoboken, NJ 07030, (201) 748-6011, fax (201) 748-6008, or online at http://www.wiley.com/go/permission.
Limit of Liability/Disclaimer of Warranty: While the publisher and author have used their best efforts in preparing this book, they make no representation or warranties with respect to the accuracy or completeness of the contents of this book and specifically disclaim any implied warranties of merchantability or fitness for a particular purpose. No warranty may be created or extended by sales representatives or written sales materials. The advice and strategies contained herein may not be suitable for your situation. You should consult with a professional where appropriate. Neither the publisher nor author shall be liable for any loss of profit or any other commercial damages, including but not limited to special, incidental, consequential, or other damages.
For general information on our other products and services please contact our Customer Care Department within the United States at (800) 762-2974, outside the United States at (317) 572-3993 or fax (317) 572-4002.
Wiley also publishes its books in a variety of electronic formats. Some content that appears in print, however, may not be available in electronic formats. For more information about Wiley and AIChE products, visit our web site at www.wiley.com.
Library of Congress Cataloging-in-Publication Data is available.
McGowan, Tom, 1950–
Biomass and alternate fuel systems : an engineering and economic guide / Thomas F. McGowan.
p. cm.
Includes index.
ISBN 978-0-470-41028-8 (cloth)
1. Biomass energy — Economic aspects. 2. Biomass energy — Environmental aspects. 3. Renewable
energy sources — Economic aspects. 4. Renewable energy sources — Environmental aspects. I. Title.
TP339.M38 2009
662′.88 — dc22
2008035476
PREFACE
WE ARE ONCE AGAIN IN an energy and fuels crisis, with costs escalating dramatically and supplies tight. This has happened before and, once again, the economy and industry will adjust to new conditions.
This book is about how to adjust to this difficult situation by using renewables for industrial applications, while cutting operating costs. In addition to providing economic benefits, the switch to renewable wood and agricultural fuels reduces greenhouse gas emissions, as these renewables are assigned a zero greenhouse emission factor and are considered “carbon neutral.”
Some of the material in this book is from The Industrial Wood Energy Handbook, written in 1984. This book is an update and expansion of that work, adding information and broadening the scope to include agricultural feedstocks and the use and production of liquid fuels such as ethanol from cellulosic (noncorn) feedstocks. It also covers fireside slag treatment (not a small issue in wood and agricultural combustion systems!), has up-to-date equipment vendor information, more detail on the furnace grate systems that are the heart of many biomass and wood combustors, and information on hot oil systems and hot air, introductory material about sustainable biomass yields, as well as the basics of greenhouse gas emissions calculation methods.
You will find this book to be useful in choosing the right equipment the first time, producing feasibility studies that define project economics, and cutting industrial fuel costs while reducing greenhouse gas emissions.
THOMAS F. McGOWAN
Atlanta, Georgia
January 2009
ACKNOWLEDGMENTS
Major contributors to this handbook are:
Thomas F. McGowan, PE, Editor, Primary author, Chapter 1 on alternate fuels, Chapter 4 on slag
William S. Bulpitt, P.E., Associate Editor, Chapter 2 on biomass sustainability
Michael L. Brown, PE, Associate Editor, Chapter 12 on wood pellet production
James L. Walsh, Jr., Associate Editor, Chapter 4 on equipment vendors
Dennis Coughlin, Doug McLain, and Craig Smith, Chapter 1 contributors on alternate fuels
Tom Wechsler, Chapter 1 contributor on alternate fuels, Chapter 4 on hot oil and hot air systems and grates
Jonathan Scurlock, Chapter 2 on fuel properties and combustion theory
Ryan Melsert, Chapter 3 on liquid fuels, Chapter 11 on economic analysis, appendices 1 and 2 updates, book production
We are grateful for the assistance of the following in preparation of this handbook: Haeja Han, Publisher and Executive Editor, Technical Publications, AIChE; Robert Esposito, Wiley Publishing; John Wells and Devon Dartnell, Georgia Forestry Commission; and Sam McGowan, graphics.
Acknowledgements from The Industrial Wood Energy Handbook
Major Contributors to the 1984 Industrial Wood Energy Handbook: William S. Bulpitt, Grant B. Curtis, Jr., Steven J. Drucker, Michael L. Brown, Robert J. Didocha, Thomas F. McGowan, James L. Walsh, Robert D. Atkins, and Dr. Badarinath S. Dixit
The following assisted in preparation of the 1984 Industrial Wood Energy Handbook:
John C. Adams, Jr., Michael S. Smith, David E. Harris, F. Dee Bryson, Anthony D. Jape, Douglas Davis, Bryan Miller, William Hartrampf III, Joseph Saucier, David Lapin, Dr. Arthur Shavit, David Pugmire, and Joanne Bocek
The 1984 Industrial Wood Energy Handbook was written under Contract Number DE-FG05-79-ET 23076, which was funded by the U.S. Department of Energy.
CHAPTER 1
INTRODUCTION TO ALTERNATE FUELS
INTRODUCTION
Fuel costs rose sharply in 2005 due to hurricane damage to offshore platforms and refineries in the Gulf of Mexico. This was followed by a drop in the strength of the U.S. in dollar in 2007 and 2008, international developments in the oil supply, and increased demand. Competing fuels—coal and natural gas—rose in price in lockstep. Natural gas has risen in cost, and has been reported by clients to be as much as $17/MM Btu for industrial use in the northeast, and the cost of a 42 gallon barrel of oil hit $140, which is $3.33 per gallon just for the raw material.
Operating firms with fuel bills that are a high percentage of their costs are seeing profit margins erode, and one solution to the problem is fuel switching and use of alternate, sometimes overlooked, lower cost fuels.
There are many alternate fuels available to replace the big three—gas, oil, and coal. These include biomass, in particular, wood, but also including bagasse, fast growing switch grass, agricultural feedstocks, and used cooking oil. Other alternate fuels are covered in this book as a point of comparison and in less detail than biomass, and also because they may be cofired with biomass fuels. They include used/recycled oil, tires, and solid waste.
Parts of this chapter were excerpted by special permission from Chemical Engineering, March 2006. Copyright © 2006 by Access Intelligence, New York, NY 10038.
Some combustion systems were set up for multifuel firing and can be easily changed over, whereas others can be refitted and adapted to new fuels.
Heat recovery is the other option—adding heat exchangers to current processes, or changing over to new types of equipment, for example, from an elevated flare to a thermal oxidizer with a heat recovery boiler to recoup useful heat. This approach can be used to cut greenhouse gas emissions while saving on fuel costs.
This section covers the heating value, costs, and other properties of alternate fuels and fossil fuels, the changes required to fire alternate fuels, and options for heat recovery. It also addresses in brief the regulatory aspects of fuel switching and impacts on emissions. In addition to information on the use of alternate fuels, this section also covers production of secondary fuels from biomass feedstocks, for example, ethanol from cellulosic feedstocks and transportation fuels from agricultural feedstocks.
WHAT FUELS ARE USED?
Conventional fossil fuels rule the marketplace. They include natural gas, propane, fuel oil, and coal. Alternate fuels include:
Table 1-1 shows heating values and costs for industrial use of alternate fuels and selected fossil fuels, which are the benchmark for comparison on prices and heating values. Establishing a fuel price is not as simple as it might seem, as database figures must be adjusted to match the application, location, and time of year, and taxes, transport, broker fees, and market must be taken into account to come up with representative prices paid by the end user. The type of contract, for example, interruptible service for natural gas, also affects final price. Many databases show current, 30 day spot pricing. An example is the NYMEX (NY Mercantile Exchange), which showed natural gas in the $15/MM Btu range on 12/8/05. This price is based on the Henry Hub in Louisiana, and does not include delivery and markup. This is a higher price than that found in longer-term contracts, which tend to smooth out short-term spikes and dips. Based on EIA data, the Henry Hub price for natural gas went up 63% from January 04 to January of 2009 (projected price). For more on forecasting and market movements see www.eia.doe.gov/emeu/steo/pub/contents.xhtml, and for relationships between gas and oil see www.dallasfed.org/research/swe/2005/swe0504c.xhtml.
Table 1-1. Heating values and costs for fuels
Notes: EIA, http://www.eia.doe.gov/; Timber Mart South/UGA, Tom Harris, 12/6/05; RB Rubber Products, Pete Daly, 503-283-2261, Portland, OR.
Biogas (from wastewater treatment, conversion of manure, and from biological degradation in landfills) and plant and refinery gas are confined to use on-site or a short distance off-site and are not transportable. Setting a price for these fuels is difficult, as some of the cost may be attributable to regulatory requirements (e.g., regulations on landfill gas), whereas the rest might be allocated as internal cost to the end use. For example, most landfill gas must be collected and flared if it will not be used as a fuel for an engine or furnace. So the cost allocated for use as a fuel might be only that of any extra gas cleanup and extra fan or blower power and piping required to transport the biogas the extra distance to the engine.
Reclaimers throughout the United States produce used oil. It is frequently referred to as “spec oil,” referencing U.S. Environmental Protection Agency (EPA) terminology that allows its use as a product and takes it out of the waste category. See CRF 279.10 for more detail (http://ecfr.gpoaccess.gov, part 40, subparts 266–299) and Table 1-3 for EPA requirements. This EPA regulation also allows reuse of used oil on-site by a generator (e.g., blending with diesel fuel for use in the company’s vehicles), and under these conditions, the fuel is not subject to EPA used oil or waste regulations. Typical properties for used “spec oil” can be found in Table 1-2. The asphalt industry and industrial and utility boilers are major users of used “spec oil.”
With the exception of some cement kilns that feed whole tires, TDF (tire-derived fuel) is normally burned as chips in boilers and cement kilns. Prices range widely, based on state used-tire tariffs, number of processors, and supply/demand. TDF prices are generally similar to coal.
Table 1-2. Typical properties of used oil from reclaimer
Source: Perma-Fix, Inc., personal communication, Doug McLain, 12/5/05.
Parameter | Value |
Heating value | >135,000 Btu/gal |
Water | <1% |
Solids | <1% |
Viscosity | 90–120 SSU at 100°F |
Flash point | >100°F |
Table 1-3. EPA 40 CFR 279.11, limits for used oil specification level(1,2)
Parameter | Value |
Arsenic | ≤5 ppm |
Cadmium | 2 ppm |
Chromium | 10 ppm |
Lead | 100 ppm |
Flash point | ≥100 °F |
Total halogens | 4000 ppm(3) |
1. Used oil not exceeding any specification level is not subject to this part (40 CFR 279) when burned for energy recovery. The specification does not apply to mixtures of used oil and hazardous waste that continue to be regulated as hazardous waste [see § 279.10(b)].
2. Applicable standards for the burning of used oil containing PCBs are imposed by 40 CFR 761.20(e).
3. Used oil containing more than 1,000 ppm total halogens is presumed to be a hazardous waste under the rebuttable presumption provided under § 279.10(b)(1). Such used oil is subject to subpart H of part 266 of this chapter rather than this part when burned for energy recovery, unless the presumption of mixing can be successfully rebutted.
Coal and coke can be used in industrial equipment, and both have been fired in cement kilns [1]. Pet coke (petroleum coke) prices are in the range of that of coal. Shipping dictates that there is a price advantage for users near the refineries and coke plants that produce this material as a byproduct of heavy-oil refining. It should be noted that this material tends to be high in sulfur content, and any combustion system using it needs to have equipment capable of dealing with the SO2 emissions. More detail on pet coke can be found in the referenced EPA report [2].
Biomass fuels are becoming a more common alternative fuel source to fossil fuels as conventional energy prices rise. The primary biomass fuel is wood waste; however, bagasse (sugar cane residue), ag-fuel, or fuels derived from straw, rice hulls, and shell hulls, biomass grown as a fuel crop (e.g., switch grass) and other agricultural sources are becoming more popular. Plywood, lumber, OSB (oriented strand board), and related plants have long used bark, wood waste, planer shavings, and sander dust from plant operations to provide process heat for drying and pressing of boards rather than fossil fuels. However, biomass fuels are finding applications in nonforest products industries as well. Biomass fuels are used to replace up to 5–10% of coal during cofiring in some utility boilers at power plants. The reason for replacing only a portion of the fossil fuel is that generally wood fuels have a lower heating value and higher moisture content, so that only a portion of coal fuel can be replaced without significant loss of boiler performance and output.
Advantages to biomass are lower fuel cost and lower emissions, since wood fuels are much lower in sulfur content than most typical coals. They also contain ash, which has alkali components that can react with and remove some sulfur dioxide. In addition, in those countries that have ratified the Kyoto Protocol, the use of naturally derived fuels as opposed to fossil fuels is a common method to reduce the emission of “greenhouse gases” and obtain CO2 emission credits, since renewable fuels from plant sources are considered “CO2 neutral” under this accord. This is common in Europe and is an emerging market in itself, with wood pellet producers in the United States shipping their product across the Atlantic. Fossil fuels are burdened with associated CO2 greenhouse gas emissions. Although company-wide studies can cost thousands of dollars to count direct and indirect CO2 emissions, when it comes to burning a fuel, the math is really quite simple: Multiply the fuel weight per year by the carbon fraction of the fuel, then multiply by 3.66 (3.66 is the molecular weight of CO2 divided by that of carbon) and divide by 2000. This result is the tpy (tons/yr) of CO2 generated. The carbon fraction in the fuel can be found in reference texts or via lab work. Basic chemistry can also be used to calculate the carbon fraction. For example, for methane, the carbon weight is 12, when divided by the total weight of 16, the result is 0.75, or 75% carbon.
COMBUSTION ISSUES AND APPLICATION TO EQUIPMENT
Burning alternate fuels requires going back to the basics. We have to know fuel properties, as the chemistry of the fuel dictates the final stack-gas flow and products of combustion. For example, higher sulfur will mean more SO2 generated, and for some fuels, such as wet wood hog fuel, higher excess air (in the range of 50%) is required using air swept stokers, much more than for oil and gas, which are usually in the 15–25% range, or lower when O2 trim or mass flow control is used.
Application to Equipment
Some equipment is easy to alter for firing of alternate fuels. For example, boilers set up for natural gas are also sold with gas/oil firing systems. Installation of oil tankage, fuel trains and atomizers, and substitution of an oil gun for the gas spud may be all it takes to change over. Changing from No. 2 fuel oil to heavy oil or reclaimed used oil will require the addition of steam or compressed-air atomizers and oil-heating equipment.
Changing to solid fuel is much more difficult. For example, compact boilers set up for gas/oil are simply not compatible with solid fuel firing, unless a gasifier is used to convert the fuel upstream. Very large dryers and calciners are more amenable to such a change, as they were designed to handle particulate matter, and have pollution control systems that remove particulates. Some manufacturers are working on a new generation of mid-sized (100–200 MM Btu/hr) pulverized coal burners to respond to emerging markets and applications that can tolerate particulates.
For larger, long-term commitment to solid fuels, the best fix may be the purchase of new equipment designed for its use.
Beware that some elements in fuels can cause major problems even in small amounts. These include sodium and potassium that can form low melting point ash, and sulfur and chlorine that form acid gases. An additional issue is fuel bound nitrogen, which forms NOx. These problems can cause equipment outages due to fouling and corrosion, and raise emissions.
One issue with biomass fuels is their alkali ash compounds, which form salts in the combustion process and/or may lower the ash softening points, causing fireside fouling problems. This is particularly true with agricultural biomass, while wood-based biomass has lower alkali concentrations when compared to many agricultural feedstocks. Still, for any biomass fuel, it is advisable to analyze for alkalis, and make a determination of the fuel’s fouling and slagging potential. Also, any heat recovery equipment must be properly designed to minimize the potential any of these fuels have for fouling. Fireside additives have been used, generally with good effect, to reduce fouling problems and slagging of grates.
SO2, Acid Gas Dew Point, and Heat Recuperation
Heat recuperation is used for many processes, and more of these systems are being added today to reduce fuel costs. Higher sulfur fuels can harm heat recuperators, as heat recuperation lowers stack-gas temperatures and can cause dewpoint condensation of acid on heat exchanger surfaces, causing rapid corrosion. This is particularly an issue for air preheaters and economizers used to preheat boiler feed water via heat exchange with stack gases. Figure 1-1 addresses this subject and will help keep you out of trouble. It provides the acid-gas dewpoint based on sulfur loading in the fuel.
For example, a fuel with 20 grains (there are 7000 grains per lb) of sulfur per 100 ft3 of fuel (fuel gas) divided by the fuel heating value in Btu/ft3 of the fuel gas will have an acid-gas dewpoint of 242°F at 20% excess air. Heat exchanger wall temperatures below that will result in liquid acid on the metal surface, and heat exchangers will experience high rates of corrosion. Graphs of acid-gas dewpoint are available in many references, such as ASHRAE’s Handbook of Fundamentals [4].
Figure 1-1. Influence of sulfur oxides on flue-gas dewpoint. (Chart © ASHRAE, Handbook of Fundamentals, 1993, used with permission ASHRAE, www.ashrae.org.)
ABOUT EMISSIONS AND REGULATIONS
In brief, the regulatory problems involved in fuel switching are:
If the original permit allowed firing of other fuels (e.g., No. 6 oil as alternate to natural gas), then no repermitting is required to switch to fuel oil. However, it would be worth checking the permit application, the operating permit, any language in the facility’s State Implementation Plan (SIP) permit or Title V permit (number of hours of operation may have been limited to reduce NOx) that may need to be modified, thus requiring the facility’s operating permit to be reopened and subsequently reissued.
Furthermore, depending on whether the area in which the facility is located is in attainment or nonattainment with the national ambient air quality standards (NAAQS), coupled with the magnitude of the emissions increase that may occur as a consequence of the fuel switching, New Source Review (NSR) permitting applicability could be triggered. This could result in additional permitting complexity (beyond just simply reopening the facility’s Title V permit) that could involve additional requirements to install postcombustion controls and/or acquire internal or external emission offsets in order to permit the modification. Thus, the important first step in evaluating any project that may involve fuel switching is to first undertake a permitting analysis to assess the underlying regulatory requirements the facility is subject to, and establish the optimum path-forward permitting strategy.
Some alternate fuels emit less pollution. For example, tests with used cooking oil firing boilers showed lower CO and NOx emissions than with fuel oil. Thus, substituting this alternate fuel may require only notification to the regulators.
In the end, your relationship with the regulators is a critical element. If you have an ongoing, positive relationship, you may find that it may not take all that much paperwork to change fuels, as long as emissions do not rise past regulatory thresholds.
EPA’s AP-42 guide to emission rates may prove useful when exploring fuel switching. It contains a compilation of air pollution estimates for industrial stationary sources and other air pollution sources. It is available online, and provides emissions for various applications (e.g., boilers and cement kilns), by industry and by fuel. Useful URLs can be found in reference [4].
Note that the above discussion applies to fuels and nonhazardous waste. It does not apply to firing of RCRA “hazardous waste,” for which much more stringent rules apply and permitting can take years.
REFERENCES
[1] “Cemex, Power Play, Expensive Energy? Burn Other Stuff, One Firm Decides,” John Lyons, The Wall Street Journal, September 1, 2004, Page A1.
[2] EPA Pet Coke report, 1999, www.epa.gov/ORD/NRMRL/pubs/600r01109/600R01109appA.pdf.
[3] ASHRAE, Handbook of Fundamentals, Mark S. Owen, Editor, ASHRAE, Atlanta, GA, 2005.
[4] U.S. EPA AP-42, emission factors, by chapter, fuel type, www.epa.gov/ttn/chief/ap42/ch01; for natural gas, including boilers, http://www.epa.gov/ttn/chief/ap42/ch01/final/c01s04.pdf; by industry, www.epa.gov/ttn/chief/ap42/.